I. Introduction
With the continuous progress of science and technology, lithium battery plays an increasingly important role in our daily life and work. As a key link in the manufacturing process of lithium batteries, the coating process is pivotal to ensuring the performance and safety of lithium batteries. However, in the actual production process, the problem of slight cracks in the coating of lithium batteries often occurs, which not only affects the aesthetics of lithium batteries, but more importantly, may have a negative impact on their performance and safety. Therefore, the purpose of this paper is to discuss the causes and response strategies of minor cracks in lithium battery coatings, in order to provide useful references for relevant enterprises and researchers.
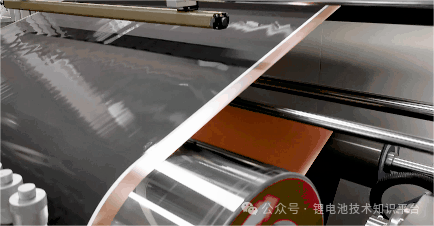
Second, lithium battery coated light fine cracks cause analysis
Problems with coating materials
Coating material is one of the key factors affecting coating quality. If the composition of the coating material is not stable, the viscosity is not moderate or the solid content is not up to standard, etc., it may lead to cracks when coating. In addition, insufficient adhesion between the coating material and the substrate is also an important reason for the appearance of cracks.
Adjustment of coating process parameters
Adjustment of coating process parameters is crucial for the control of coating quality. For example, improper adjustment of coating speed, temperature, humidity and other parameters may lead to cracks in the coating. In addition, the matching degree of each process parameter in the coating process is also an important factor affecting the coating quality.
Problems with equipment
Problems with the coating equipment may also lead to the appearance of coating cracks. For example, improper control of parameters such as the surface roughness of the coating rollers and the pressure between the coating rollers and the substrate may affect the coating quality. In addition, improper maintenance of equipment or aging of equipment may also lead to the appearance of coating cracks.
Environmental factors
Environmental factors may also affect the coating quality, such as the environment of the temperature, humidity and other parameters are not properly controlled, may also lead to cracks in the coating. In addition, environmental contaminants such as dust and impurities may also have a negative impact on coating quality.
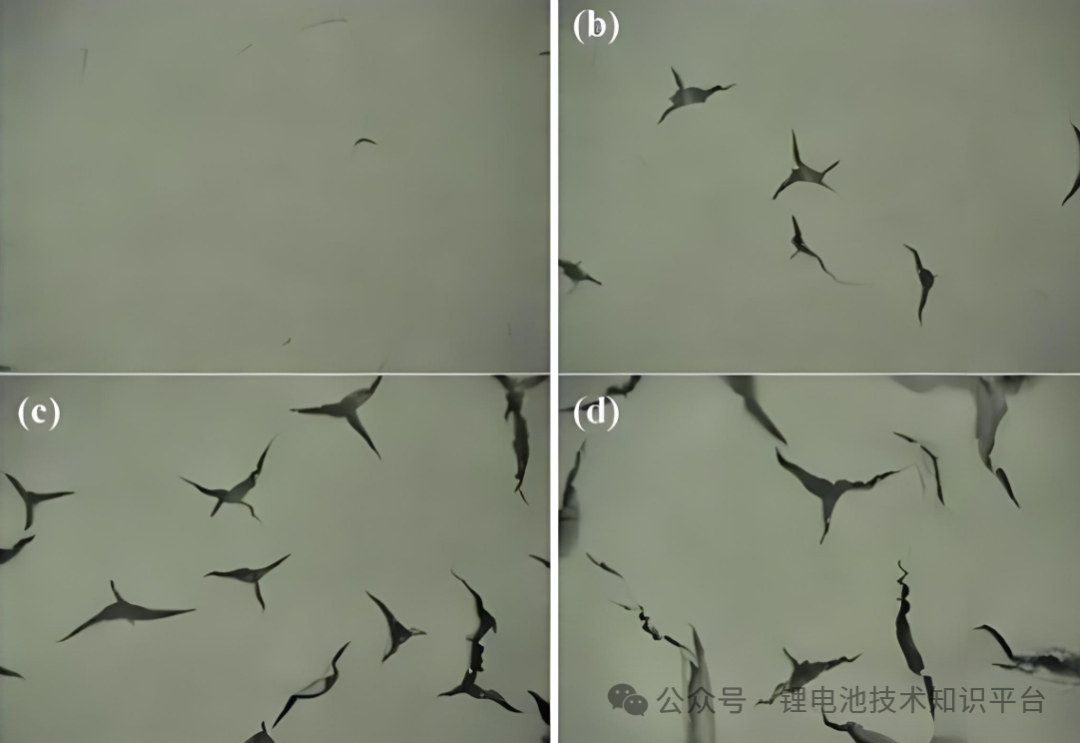
3. Coping strategies
To address the above problems, we can start from the following aspects to solve:
- Strictly control the quality of coating materials
Select coating materials with stable quality and excellent performance, and strictly control their composition, viscosity, solid content and other parameters to ensure the coating quality. In addition, the adhesion test between the coating material and the substrate should be strengthened to ensure that the adhesion between the coating material and the substrate meets the requirements.
- Adjustment of coating process parameters
According to the actual situation, the coating process parameters should be adjusted reasonably, such as coating speed, temperature, humidity, etc., in order to ensure the coating quality. At the same time, should strengthen the matching degree of adjustment between the process parameters, in order to improve the coating quality.
- Ensure the good condition of equipment
Regular inspection and maintenance of coating equipment to ensure that the parameters of the equipment in a normal state, such as the surface roughness of the coating roller, the pressure between the coating roller and the substrate. For aging equipment should be replaced or upgraded in a timely manner to ensure the stability and reliability of the coating process.
- Control of environmental factors
Reasonable control of environmental factors, such as environmental temperature, humidity, etc., to ensure the quality of coating. At the same time, the cleanliness of the workshop should be strengthened to reduce the dust, impurities and other pollutants on the coating quality.
- Strengthen quality inspection
In the production process, strengthen the quality inspection to find and solve potential problems in time to prevent batch problems. Automatic testing equipment or artificial testing means can be used to monitor the coating quality of lithium batteries in real time, once found that the quality of minor cracks and other quality problems should be adjusted and repaired in a timely manner.
*** Translated with www.DeepL.com/Translator (free version) ***
4. Conclusion
Through the above analysis, it can be seen that the reasons for the slight cracks in the lithium battery coating are manifold, including coating materials, process parameters, equipment and environmental factors. In order to effectively solve this problem, it is necessary to strictly control the quality of coating materials, adjust process parameters, ensure that the equipment is in good condition, control environmental factors and strengthen the quality of testing. Only in this way can we effectively improve the coating quality of lithium batteries and enhance the performance and safety of lithium batteries. At the same time, this also requires the relevant enterprises and research institutions to strengthen the investment in technology research and development and innovation, and constantly improve and optimize the coating process, to promote the sustainable and healthy development of the lithium battery industry.